RFIDHYSystème de véhicules guidés en rail
Ce système est un système de tri des palettes conçu pour fournir un actif à haut débit. Manipulation en combinaison avec un système de stockage et de récupération automatisé (entrepôt automatisé). Le RGV est capable de trier sur plusieurs ceintures de convoyeur. Permettant un accès efficace à et depuis plusieurs entrepôts automatisés, vers et depuis la cueillette des stations. Et tri par direction d'expédition. Il permet également la gestion du stockage du froid, Le rendre idéal pour l'automatisation de la chaîne froide.
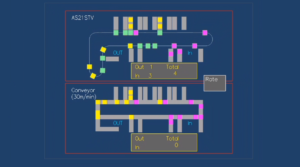
RGV
Haut débit
Le RGV se déroule en douceur et tranquillement. Avec une vitesse de voyage maximale de 200 m / min et une vitesse de transfert de charge de 30 m / mon. La vitesse de chaque véhicule est automatiquement ajustée en fonction de son emplacement et de l'état réel de la cargaison. En boucles et double systèmes avec plusieurs véhicules. Le contrôleur optimise l'allocation des véhicules pour éviter l'excès de mouvement et la consommation d'énergie. Optimisant ainsi l'efficacité globale du système.
Souple
Le système est disponible en une seule shuttle, Configurations à double shuttle ou en boucle pour s'adapter à diverses dispositions de construction. Différentes exigences de volume d'espace et de trafic. Le système est également très évolutif. Par exemple, Extension de la piste pour s'adapter aux entrepôts plus automatisés. Ou selon le débit, augmenter ou diminuer le nombre de véhicules.
Fiable
Lorsqu'un convoyeur est utilisé, Les palettes sont déplacées sur le convoyeur en raison de l'inertie. Ce problème est particulièrement visible lorsque la charge sur la palette est lourde.
Avec notre système RGV, Les véhicules chargés de palettes se déroulent bien sur la piste. Et il existe un système de renforcement supplémentaire pour assurer le transport de fret lisse et stable. Aussi, À l'exception des systèmes à une seule buttle. Les travaux de maintenance peuvent être effectués pendant l'exécution du système.
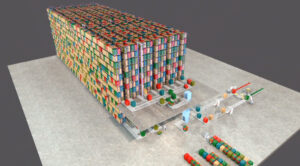
RGV
Modifications de mise en page
Nous offrons les trois types de systèmes suivants en fonction du volume et des opérations de votre entreprise.
Système de navette unique
Les vélos voyagent dans les deux sens sur des voies droites pour transporter les fournitures. Cela signifie. À l'autre, Augmentation de la productivité.
Les rails droits peuvent être combinés avec des rails incurvés à 90 ° pour former une disposition en L. Cela fonctionne bien lorsque la disposition des bâtiments et de l'équipement de production est difficile à configurer avec une disposition en ligne droite.
Système de navette double
Le système se compose de deux chariots sur une piste droite, qui peut fonctionner simultanément. Entraînant une augmentation de 1,5x du débit par rapport à une seule navette.
Nous pouvons également déconnecter un véhicule de la zone d'évacuation et exécuter le système avec un autre véhicule. Ce qui est utile comme sauvegarde si l'un des véhicules échoue.
Système de circulation multi-véhicules
Plusieurs véhicules sont déployés sur une voie circulaire composée de rails droits et de rails incurvés en U. Chaque véhicule peut transporter une charge en même temps, qui peut gérer plus de charges qu'un système de navette.
Des véhicules supplémentaires peuvent être ajoutés à un stade ultérieur pour augmenter la capacité de traitement. Si le volume de marchandises à traiter devrait augmenter à l'avenir. Le cycle peut également être élargi pour accueillir des grues supplémentaires dans l'entrepôt automatisé. Rendre très évolutif pour répondre aux demandes d'une entreprise en croissance.
Dans le cas de l'entretien des véhicules, Les véhicules affectés peuvent être déplacés vers un dépôt d'entretien à l'extérieur de la boucle. Permettre aux véhicules restants de continuer à fonctionner.