RFIDHY team has an in-depth understanding of the needs of each department. Product attributes and environmental constraints, develops applications that meet the needs of steel mills. And is able to control the quality of RFID use. Moreover, the company continues to overcome technical difficulties during the testing process.
Transportation needs of the steel industry
In the steel industry, steel products are made of metal and the ambient temperature of the factory is high. Therefore, in this field, the use of RFID has many technical limitations.
RFID is being used previously, rolling mills used low-cost bar codes to read product material information. Barcodes have limitations such as reading direction, distance. And data storage capacity. In addition, barcode labels are susceptible to operating environmental conditions. And labels are also susceptible to damage during handling. While the cost of barcodes is low, it incurs many intangible costs in use. For example, because read rates are affected by many factors such as environmental conditions and processing. When readers cannot read information, it takes employees a lot of time to find unread products. As a result, in the past, trucks were often jammed at transport checkpoints in the transport system. And these issues affected the production capacity of the production line.

Figure 1 Inspection station personnel use barcode readers to confirm product information
Image description: Barcodes have distance limitations in the app.
Therefore
A worker holding a reader needs to be very close to the barcode label on the product to read the data.
However, steel companies’ products are bulky, extremely heavy, and move frequently. Making it difficult to read data during barcode use. The space of steel companies can be said to be an inch of land. In order to make the application of factory space more cost-effective. The company plans to move the finished product warehouse out of the factory to improve the land use value of the factory.
Since the finished goods warehouse is outside the factory, the product needs to be transported from the factory twice. Due to the huge volume and weight of steel, a lot of manpower and time are required for each handling. And products are collided and damaged during handling. Which delays the manufacturing process of the production line and causes production to stop. Therefore, it is necessary to improve the smoothness of the transportation system. In the past, rolling mill transport employees often needed to climb onto trucks to check for unread labels and items. Which not only blocked transport routes, but also created safety concerns.
Some employees had accidents while checking barcode data because they were worried about delays in shipping. Employee safety is invaluable. To avoid similar work accidents, steel companies must improve their cargo inspection processes.
RFIDHY’s research and development of RFID has achieved fruitful results
The steel mill developed by RFIDHY is waterproof and high temperature resistant, free from metal interference with RFID chips.
Part of the transport process has been successfully introduced.
In addition to the breakthrough in wafer design. The focus of application design is not to increase the workload of the staff and not to change the process.
At present, customers who purchase products downstream still use the barcode system. So the products of the steel company are used RFID. The employees of the production department will attach two labels to the finished product before leaving the factory. Onto the truck.
Integrating RFID to integrate the tag installation and use process into existing operations. The introduction process can minimize friction without increasing employee workload.
Process innovation
RFID process innovation (Process Innovation) technology can make companies more centralized resources, effectively use data. And reduce management costs, but users need to spend time learning and adapting to the operation mode. Which can easily make employees have a negative attitude towards new technologies.
Iron and steel companies also have this consideration. So on the one hand, in the use of RFID, strategically, the application of RFID in the transportation system is relatively simple. And the intangible costs such as manpower training during the introduction are relatively low. Which improves the overall efficiency of the production line. So the strategic risk of importing RFID in the transportation system is low.
In addition, the successful application of the transportation system can improve the confidence of various departments. Which will help the application development of RFID steel companies in various departments.
RFID Enhances Information Flow in Steel Company’s Transportation System
In the past, steel company products needed to be transported from the factory to the finished goods warehouse. And could not be delivered directly to the company that purchased the product.
The implementation of RFID technology in the transportation system not only saves manpower and time. But also products can be directly transported from Steel Plant to downstream purchasing companies. Reducing the cost of one-time processing and one-time transportation.
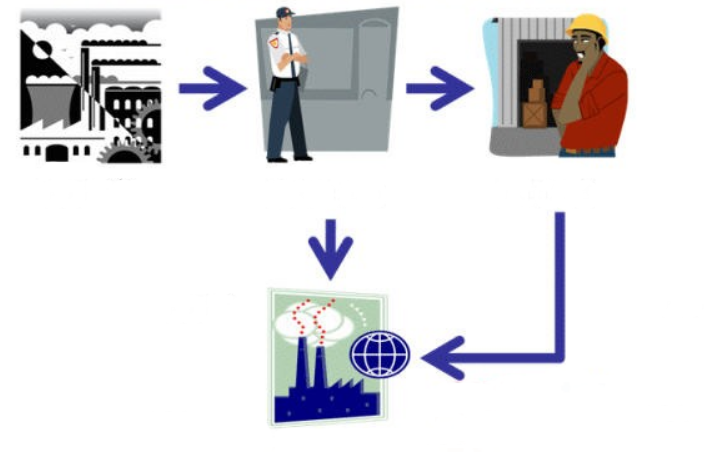
Figure 2 Steel transport system
After switching to RFID tags, employees of the steel company read the passive RFID tags hanging on the products to understand the product. Size, weight, quantity, total weight and other information. And read the RFID passive tags on the truck (as shown in Figure 3) to obtain Vehicle information. Put all the information on the mobile checklist and hand over the checklist to the mobile driver.
In the past
Before the application of RFID, the steel company did not move to the outpost. And the truck was directly sent to the steel product warehouse.
After RFID, steel companies can open an external handling list at the factory (as shown in Figure 4). And many products can be shipped directly to customers, simplifying the transportation process and improving transportation efficiency.
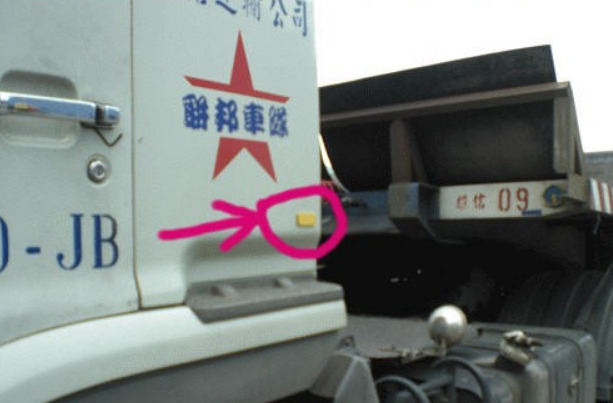
Figure 3 The yellow one on the vehicle is a passive RFID tag
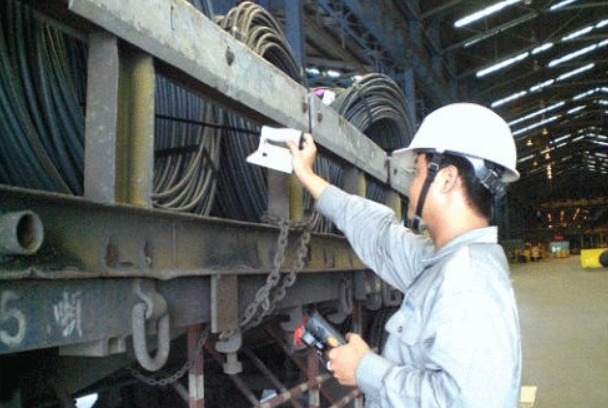
Figure 4 Moving the checkpoint outside the factory gate
Immediately after leaving the factory, the driver goes to the checkpoint at the entrance of the factory.
When the truck approaches the checkpoint, a few seconds after the reader receives an RFID. The vehicle data of the active tag (Figure 5) is displayed on the front LED on the Kanban at the checkpoint. And the inspector can quickly confirm that the vehicle data is correct.
Inspectors can check the data entered by the personnel at the data inspection post. And the inspection data is consistent with the data previously moved outside the factory gate.
RFID data cannot be read normally, and personnel can also use the mobile checklist for confirmation.
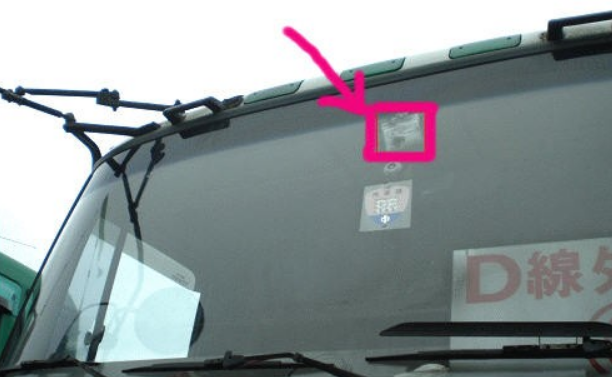
Figure 5 Active RFID tag on the front of the truck
The inspection station at the entrance of the factory uses RFID to check product information. When the vehicle passes through the inspection station, the inspection process is fully automated. And there is no need for drivers or inspectors to use the reader to get close to the product to obtain information. Which can improve inspection efficiency and eliminate the need to confirm and manually fill in the information one by one. Improve the accuracy of information and ensure the safety of transport personnel.
The original inspection process took 90 seconds.
Only 18 seconds after RFID, the traffic jam problem in the transportation system is significantly reduced.
Save management costs
RFID technology can save a lot of management costs, avoid industrial safety accidents and product damage caused by multiple handling.
This application is a major breakthrough in the steel industry. And will continue to invest in research and development of RFID application improvement in the future.
Application development of future steel companies
The company’s future goal is to expand the scale of RFID applications in two application directions. One is to expand from the initial online product to other products of the steel company. The other is to promote it to downstream purchasing customers.
In addition to wires, steel companies have hot-rolled and cold-rolled products. Which are several times more than wires. In the future, using RFID to transport these two products can increase the value of RFID technology. RFID applications can reduce tags unit cost.
Externally, if downstream purchasing customers can use RFID, the overall value of the iron and steel company’s supply chain will be high. And the effect of 1+1>2 will be achieved.
The breakthrough and development of steel companies in RFID applications can be a booster for RFID to inject into the market.
Keyword: RFIDHY Warehousing NFC tag RFID Solutions